Cov-19 stimulates the application for end-use products
27/04/2020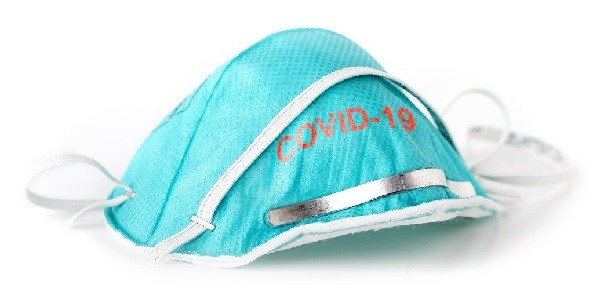
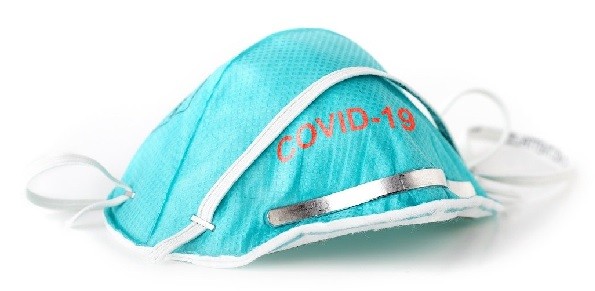
Cov-19 could draw further attention to AM, because it allows the flexible manufacturing of products in times of supply chain disruptions.
Additive Manufacturing has been a buzzword in the manufacturing industry since the introduction of the technology. In the early stage, FFF (Fused Filament Fabrication) technologies attracted large attention from individual users with its easiness of printing and cost-effectiveness, contributing to the popularization of AM technology.
In the meantime, other various AM technologies, such as SLS, SLA, PolyJet, MJF, and DLS/CLIP, have increased their shares in the manufacturing industries, appealing with their specific advantages in various applications. Cov-19 could draw further attention to AM, because it allows the flexible manufacturing of products in times of supply chain disruptions.
After years of focusing on efficiency gains, the topic finally reached mainstream supported by the increasing use of various technologies in additive manufacturing. Especially powder and resin materials are expected to have high growth rates in upcoming years. Facts and figures
Today, the global AM material market is already estimated at around 15,000 tons. ABS and PLA together account for more than 50% of the entire material market, but the share of metals is also significant. Within the next years, resin materials, such as acrylates, are expected to have the highest growth rates of all materials with a CAGR of 16-18%, while powder material, such as TPU and PA12, will grow slightly slower with a CAGR of 13-15%. Such an increasing demand for those materials shows that an increasing number of applications are integrating additive manufacturing into their production process.
The advancement of both AM technologies and materials led to the situation in which AM is used for the production of functional parts and not just for prototypes or tools. The possible optimization of production processes and innovative products by introducing AM has encouraged more and more industrial companies use AM in their production. Some industries in focus
In the footwear market, big names such as Adidas, Nike, New Balance, and Reebok, launched products which are partially produced by additive manufacturing. Various materials are of use in printing the parts of footwear, such as TPU powder, Nylon Powder, and polyurethane resin. For example, by using AM materials, including resin materials, complex structures can be easily printed at lower cost. SuP could identify that there is a broad room for novel materials, as main motivation of footwear producers is bringing innovative products to the market. A further perfect example showing how AM can solve an existing problem is the dental industry. There, AM is considered as an ideal alternative to substitute the traditional way of printing dental models - from gypsum, which often handmade and long processing – to quick manufacturing customized products, at a reduction of labor costs, better quality and accuracy of dental models. Especially resins, such as acrylates and urethane-acrylates, are increasingly demanded in the dental industry. Following the trends, several material manufacturers introduced specialized resin products for dental application. How AM could lead to a more decentralized production landscape in the future could also be observed by how much attention AM gains in the current combat with Cov-19. Due to the rising number of the patients of Cov-19, hospitals and medical professionals are struggling with the shortage of personal protective equipment (PPE). In the situation of urgent needs for more PPE, additive manufacturing firms jumped in printing PPE, as traditional manufacturers are overwhelmed in coping with the exploding demands for the products. The manufactured PPEs by additive manufacturing include mask adjusters, face shields, respirator valves, and so on. An Italian 3D-printing company, Isinnova began to print the replacement valves with PA12 powder to supply to the hospitals in Italy. Carbon began to print the plastic parts of face shields and swabs for cov-19 test kits with liquid resin. This example shows how additive manufacturing can play an important role as alternative when the traditional manufacturing system cannot meet the needs in the market.With the comprehensive understanding about value chain steps and rich contacts with main players in the global AM market, SuP can be your right partner in setting a strategy from market entry to business expansion. © Schlegel und Partner 2020
In the meantime, other various AM technologies, such as SLS, SLA, PolyJet, MJF, and DLS/CLIP, have increased their shares in the manufacturing industries, appealing with their specific advantages in various applications. Cov-19 could draw further attention to AM, because it allows the flexible manufacturing of products in times of supply chain disruptions.
After years of focusing on efficiency gains, the topic finally reached mainstream supported by the increasing use of various technologies in additive manufacturing. Especially powder and resin materials are expected to have high growth rates in upcoming years. Facts and figures
Today, the global AM material market is already estimated at around 15,000 tons. ABS and PLA together account for more than 50% of the entire material market, but the share of metals is also significant. Within the next years, resin materials, such as acrylates, are expected to have the highest growth rates of all materials with a CAGR of 16-18%, while powder material, such as TPU and PA12, will grow slightly slower with a CAGR of 13-15%. Such an increasing demand for those materials shows that an increasing number of applications are integrating additive manufacturing into their production process.
The advancement of both AM technologies and materials led to the situation in which AM is used for the production of functional parts and not just for prototypes or tools. The possible optimization of production processes and innovative products by introducing AM has encouraged more and more industrial companies use AM in their production. Some industries in focus
In the footwear market, big names such as Adidas, Nike, New Balance, and Reebok, launched products which are partially produced by additive manufacturing. Various materials are of use in printing the parts of footwear, such as TPU powder, Nylon Powder, and polyurethane resin. For example, by using AM materials, including resin materials, complex structures can be easily printed at lower cost. SuP could identify that there is a broad room for novel materials, as main motivation of footwear producers is bringing innovative products to the market. A further perfect example showing how AM can solve an existing problem is the dental industry. There, AM is considered as an ideal alternative to substitute the traditional way of printing dental models - from gypsum, which often handmade and long processing – to quick manufacturing customized products, at a reduction of labor costs, better quality and accuracy of dental models. Especially resins, such as acrylates and urethane-acrylates, are increasingly demanded in the dental industry. Following the trends, several material manufacturers introduced specialized resin products for dental application. How AM could lead to a more decentralized production landscape in the future could also be observed by how much attention AM gains in the current combat with Cov-19. Due to the rising number of the patients of Cov-19, hospitals and medical professionals are struggling with the shortage of personal protective equipment (PPE). In the situation of urgent needs for more PPE, additive manufacturing firms jumped in printing PPE, as traditional manufacturers are overwhelmed in coping with the exploding demands for the products. The manufactured PPEs by additive manufacturing include mask adjusters, face shields, respirator valves, and so on. An Italian 3D-printing company, Isinnova began to print the replacement valves with PA12 powder to supply to the hospitals in Italy. Carbon began to print the plastic parts of face shields and swabs for cov-19 test kits with liquid resin. This example shows how additive manufacturing can play an important role as alternative when the traditional manufacturing system cannot meet the needs in the market.With the comprehensive understanding about value chain steps and rich contacts with main players in the global AM market, SuP can be your right partner in setting a strategy from market entry to business expansion. © Schlegel und Partner 2020
Download: AM and Covid-19.pdf, 384388 kB